Designing Minds and Building Communities at Virginia Tech
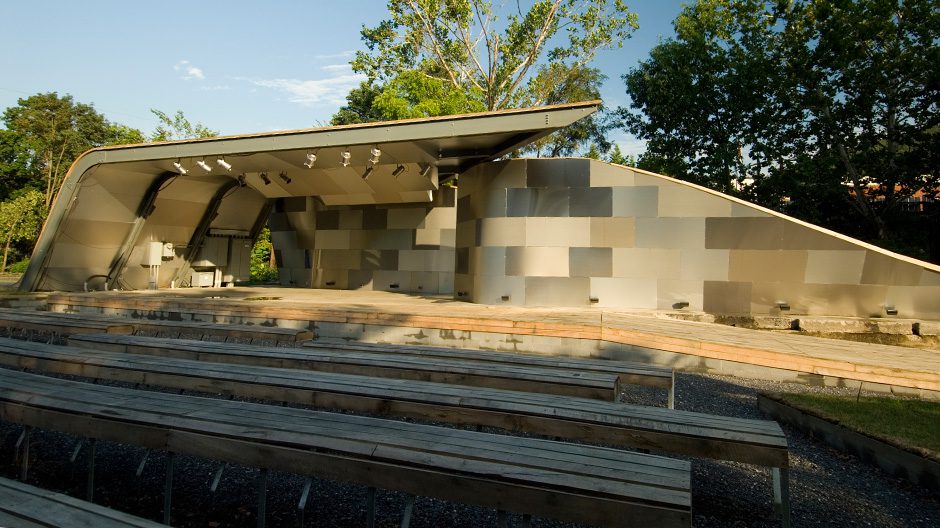
Masonic Amphitheater
Clifton Forge, VA
Project: | Masonic Amphitheater |
---|---|
Location: | Clifton Forge, Virginia |
Fabricator/Installer: | design/buildLAB at Virginia Tech School of Architecture + Design |
Architect | design/buildLAB at Virginia Tech School of Architecture + Design |
Exterior Panel Manufacturer: | ALPOLIC® |
Products: | ALPOLIC® Metal Composite Material (MCM) in zinc, titanium, aluminum and stainless steel |
Completion: | May, 2012 |
The design/build approach to architecture can be controversial, but it can provide real benefits when it leads to innovative solutions to difficult architectural challenges. Even more so when today’s architecture students – tomorrow’s professional architects – are learning to be the problem solvers. The Masonic Amphitheater in Clifton Forge, Virginia, is a perfect example, and ALPOLIC is proud to have contributed to it.
Architecture isn’t just about physical form and function. Consider the Masonic Amphitheater, a public performance space in Clifton Forge, Virginia. It’s an acoustically efficient stage. A learning and building opportunity for Virginia Tech architecture students. A statement of the innovative power of the design/build process. A gift that helps transform an industrial brownfield into a vital community center. It’s the American-Architects Building of the Year for 2012, and ALPOLIC is proud to have been an essential part of it.
Complementing the nearby Historic Masonic Theater – a Beaux Arts opera house built in 1905 – the new Masonic Amphitheater sits on a space formerly occupied by a truck tire warehouse. The old facility was dismantled, and the salvaged materials reused to build the Covington Farmer’s Market, while the remaining concrete plinth became the foundation for the Masonic Amphitheater. Both projects were designed and constructed by students in the design/buildLAB, an architecture studio at the Virginia Tech School of Architecture + Design.
Keith Zawistowski, who partners with his wife Marie Zawistowski to guide the design/buildLAB, says that the acoustic design of the amphitheater stage was crucial to the success of the project. The band shell, he explains, was designed for optimal projection of natural acoustics. Flat surfaces and right angles are anathema to uniform, uncolored sound projection, so the acoustic design called for complex geometrical shapes.
To effectively push sound from the stage out to the audience, the acoustic design called for these complex forms to be constructed of metallic surfaces backed by an acoustically neutral core. “We looked at lots of different options,” Zawistowski says, “thinking maybe we’d laminate sheet metal to plywood or something like that.” But fabricating panels in this way – especially in the required geometries – threatened to be prohibitively difficult and expensive.
The team looked for an existing product that would simplify fabrication while providing the composition they were looking for to achieve optimum acoustics. They found a perfect fit in ALPOLIC/fr Metal Composite Material (MCM) panels.
“The ALPOLIC panel was really excellent,” Zawistowski explains, “because it already had a kind of highly reflective surface on both sides and a solid core material, so it actually turns out to be a really good acoustic reflector. It had all the properties of the thing that we would otherwise be trying to custom-make.
“And it turns out to be pretty nice stuff too.”
As a student project intended to beautify and revitalize the community, the Masonic Amphitheater was made possible by generous donations of time, money and materials. ALPOLIC MCM panels were among these donations – leading to a striking visual feature that wasn’t part of the original architectural vision.
Rather than supplying panels all of a single type, ALPOLIC suggested using a combination of zinc, titanium, aluminum and stainless steel panels. This allowed ALPOLIC to donate excess panels from the end of production runs – panels that would otherwise have gone for recycling. But more important than saving costs, the multiple panel shades allowed students to create what Zawistowski describes as a “mottled” texture: “It gives it a distinct character that it wouldn’t have if it were just sort of a homogenous gray. And they’re all natural metals, as opposed to painted finishes.”
Students designed the complex geometry of the amphitheater’s band shell using 3D modeling software, and then fabricated the panels themselves using the school’s five-axis CNC router. Each panel was coded according to its placement, and then all the panels were brought to the site and screwed together to create the complex tiling pattern that is essential to the building’s look as well as its acoustic performance.
It’s no exaggeration to say that the particular beauty and sound of the Masonic Amphitheater would not have been possible without the acoustic qualities, easy fabrication and stunning appearance of ALPOLIC MCM panels. Not to mention the intelligence and hard work of the architecture students who designed this remarkable project and helped build it with their own hands – taking it from concept to reality.
Learn more about Virginia Tech’s design/buildLAB and watch “Reality Check” – a short film that documents the entire Masonic Amphitheater project from inception to completion. It’s available for free on-line streaming. Following design/buildLAB students as they discover new architectural possibilities could give you the inspiration you’re looking for to transform your next project.